Operation
The TBV-PR integrates temperature control and pressure relief into one valve. The thermal actuator of the thermal bypass valve precisely adjusts the opening based on temperature fluctuations to control flow and ensure optimal system performance. Cooler fluid goes through the valve bypass, while hotter fluid goes through the system’s heat exchanger/cooler.
The built-in pressure relief function safeguards the system from excessive pressure buildup. When the pressure exceeds a predetermined threshold, the valve opens, allowing fluid to escape and reducing pressure to a safe level. Refer to the Bypass Mode with H/X path blocked graphic below.
This versatile valve can be incorporated into a 4-way manifold to efficiently direct fluid flow based on temperature, ensuring optimal system performance and safety.
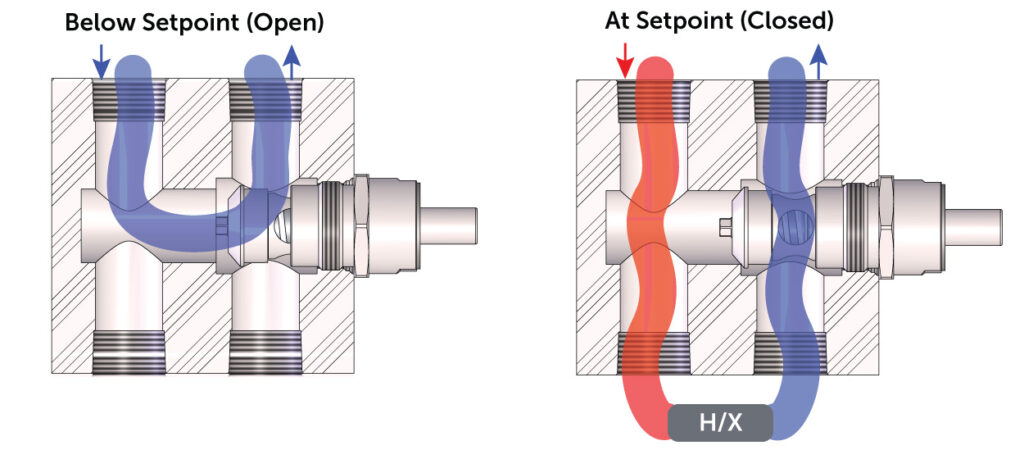
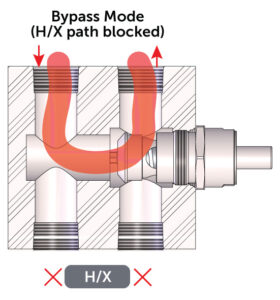
Typical Thermal Bypass Applications
- Cooling Water Control for Radiator or Heat Exchanger
- Electronics System Cooling
- Engine and Compressor Cooling System
- Hydraulic Fluid or Lube Oil Cooling Systems
- Hydraulic Power Units (HPUs)
- Hydraulic or Lube Oil Thermal Bypass
- Loop-type Circulation Systems
Design Features
- Exclusive self-actuating Thermoloid® thermal wax actuator
- Integrated pressure relief
- Standard valve material is brass or stainless steel
- Reactive, compact, and low mass – fast response
- Corrosion-resistant, long service life
Benefits
- Self-operating – no external power source required
- Temperature control – controls fluids by sensing over-temperature thermal levels
- Built-in pressure relief simplifies installation and maintenance processes
- Wide temperature range available
- Minimal maintenance needed
- Few moving parts – reduce system wear
Ordering
| |
| SAE-18-TBV-PR-XXX-C360-B-XXX |
| SAE-18-TBV-PR-XXX-SS-B-XXX |
| SAE-18-TBV-PR-XXX-S6-B-XXX |
Operation
ThermOmegaTech’s STVM® washdown station incorporates unique Venturi mixing technology to deliver water at the required temperature quickly, quietly, and on demand. Cold water enters the upper chamber of the mixing valve, while incoming steam enters the lower chamber. Mixing occurs as the two vortices collide, thoroughly mixing and heating the water through a Venturi diffuser with minimal noise and vibration.
Conventional washdown mixing stations that rely on multiple moving parts and use old spool and diaphragm technology are prone to premature failure due to mineral deposits and scaling. The necessary regular maintenance of these units to keep them running safely is very time-consuming and costly. The rugged STVM® mixer is unique because it has only one moving part, a thermal actuator within the mixing valve cartridge.
The patented mixing design ensures extended, uninterrupted use even if the water contains high mineral content. As the opposing vortices of steam and water enter the mixing valve, a scouring action occurs that minimizes the buildup of minerals and scale.
The Safe, Efficient Steam Water Mixing Station
An additional benefit of this design is what you don’t hear: the banging, popping, and crackling noises associated with cavitation that are prevalent in ordinary mixing stations. This smooth, quiet operation increases safety and reduces stress on the operator.
Safety is our priority, so every STVM® Washdown Station has two built-in safety features – interlocking ball valves to prevent steam-only operation and an automatic shut-off when output is 15°F over the unit’s temperature set-point (either 150°F or 185°F) or when cold water flow is interrupted.
Typical Applications
The STVM® steam and water mixer station is used for cleaning processing machinery or chemical tanks and equipment in food processing, dairy, breweries, wineries, chemical, petrochemical, and pharmaceutical facilities where high-temperature steam and cold water mixer stations are required.
Design Features
- Exclusive self-actuating Thermoloid® wax blend thermal actuator
- Interlocking ball valves prevent steam only operation
- Thermally activated over-temperature shut-off
- Unique Venturi mixing design minimizes water hammer effect
- Check valves, stainless steel thermometer, globe valves, and stainless-steel hose rack, standard with all units
- 6.5” (165.1 mm) center line to center line pipe dimension. Optional 1/4” offsets are available to adapt to existing 6.0” center line piping
Benefits
- Self-operating – no external power source required
- In-line serviceable mixing valve with easy to replace/clean cartridge – No special tools required
- Quieter operation relieves worker stress
- Resistant to the effects of mineral build-up and scaling
- Automatic steam shut-off when cold water flow is interrupted
- Optional welded Stainless Steel Station available offering superior strength and leak-free sealing for the most demanding applications
- Our stainless steel stations conform with EU Pressure Equipment Directive 2014/68/EU
Ordering
| |
| ¾” TOT (150ºF (65.6°C)) Stainless Steel Washdown Station |
| ¾” TOT (185ºF (85°C)) Stainless Steel Washdown Station |
| ¾” TOT (150ºF (65.6°C)) Brass/Bronze Washdown Station |
| ¾” TOT (185ºF (85°C)) Brass/Bronze Washdown Station |
| ¾” TOT (150ºF (65.6°C)) Welded Stainless Steel Washdown Station |
| ¾” TOT (185ºF (85°C)) Welded Stainless Steel Washdown Station |
Operation
Combining simplicity and cost effectiveness, the HCX (Hot/Cold Water Mixing Washdown Station) utilizes individual globe valves to mix hot and cold water to the desired proportion while clearly displaying the output temperature through an integrated temperature gauge.
The HCX station is available in stainless steel or brass/bronze construction and can be ordered with our exclusive SmartFlow feature. This thermostatically controlled in-line safety shutoff valve will reduce flow should the outlet temperature exceed the factory set point and shut down 10°F above that with a minimal amount of leakage. Available set-point temperatures are 125°F, 135°F, 150°F.
This unit is not designed for steam service. Please refer to our STVM® Washdown Station product sheet for steam and water mixing applications.
Typical Applications
The HCX hot/cold water mixing washdown station is used for cleaning processing tanks and equipment in food processing, dairy, breweries, wineries, and other facilities where high-temperature washdown is required. The HCX should be applied in facilities that do not have an available steam supply.
Design Features
- Exclusive SmartFlow safety shut-off option – thermostatic valve automatically stops flow should the output temperature exceed the specified set-point
- Includes hose rack, mounting bracket, and integrated temperature gauge
- Available in stainless steel or brass
- Designed to fit in place of standard industrial mixing stations
Benefits
- Self-operating – no external power source required
- Simplistic and cost-effective
- Over-temperature safety valve automatically stops flow to prevent scalding
Ordering
| |
| |
| HCX, Stainless Steel construction |
| HCX with SmartFlow, Brass construction1 |
| HCX with SmartFlow, Stainless Steel construction1 |
Operation
The ThermOmegaTech® HCS Single Channel Washdown Station is installed into a facility’s water supply line to quickly provide a high-powered single stream of either hot or cold water flow at the turn of a ball valve. The station includes a stainless-steel mounting bracket which should be used to mount the HCS in a vertical orientation so that ample room is available for adjusting valves, mounting rack, hose, and overall servicing.
A quarter-turn ball valve provides simple, yet effective control, while the integrated temperature gauge gives confirmation of outlet water temperature.
The unit is not designed for steam operation. Please refer to our STVM® Washdown Station product sheet for steam and water mixing applications.
Typical Applications
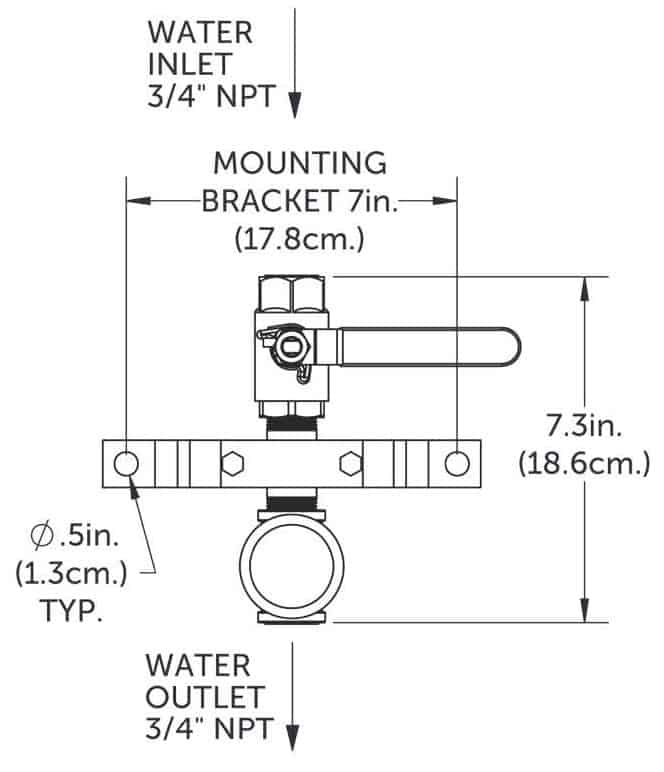
The HCS Single Channel Washdown Station is used for cleaning processing tanks and equipment in food processing, dairy, breweries, wineries, and other facilities where washdown and sanitation is required.
The HCX should be applied in facilities that need a quick and reliable supply of water in locations on the production floor.
Design Features
- ¼” turn ball valve controls user-defined hot or cold water flow
- Includes hose rack, mounting bracket, and integrated temperature gauge
- Available in stainless steel or brass
- Designed to fit in place of standard industrial single valve stations
Benefits
- Self-operating – no external power source required
- Simplistic and cost-effective
- Easy to install
Ordering
| |
| |
| HCS, Stainless Steel construction |
The MRE Washdown Station Enclosure enclosure is intended for recessed wall type installations and is flush mount which allows the doors to open a full 180° for easy accessibility.
Two separate hose racks are included to accommodate convenient access and storage for short or long hoses up to 100ft.
Design Features
- 304 stainless steel – Corrosion resistant
- Lockable 3-point door latch
- Removable hose rack for 25ft, 50ft, 100ft long hose
- Removable low mounting hose rack for 25ft, 50ft long hose
- Drain port
- Steam inlet pipe insulation supplied – Insulation must be installed
Ordering
| |
| MRE Washdown Station Enclosure, 304 SS |
Not rated for steam use. For steam hoses see Black Washdown Hose (Steam) or White Creamery Washdown Hose (Steam).
Design Features
- 4 ply textile reinforcement
- EPDM tube and cover
- Brass and Zinc plated steel swivel fittings
- Strain relief on station end
Ordering
| | | |
| 25 Ft. Black Hose Assembly | | 25 Ft. White Creamery Hose Assembly |
| 50 Ft. Black Hose Assembly | | 50 Ft. White Creamery Hose Assembly |
| 75 Ft. Black Hose Assembly | | 75 Ft. White Creamery Hose Assembly |
Steam Water Mixing Valve Cartridge Operation
A steam and water mixing valve creates hot water when cold water enters the valve and moves from the inside out, while incoming steam moves from the outside in. Mixing occurs as the two flows collide, thoroughly combining and heating the water to the desired temperature.
Because of the unique mixing characteristics inside the STVM® steam mixing valve, it is capable of mixing steam and water without the usual noise and vibration associated with other types of mixers, eliminating operator stress, and making it ideal for workplace environments.
The unique flow characteristics of the vortices inside the valve create a scouring action that minimizes the effects of mineral deposits on the valve, assuring increased service life even under adverse conditions. As a safety feature, the thermal actuator in the valve outlet is designed to turn off the steam flow into the valve if the cold water flow into the valve is interrupted.
The STVM® cartridge for our STVM® industrial steam water mixing valves can be replaced in an installed station in minutes by simply unscrewing the cartridge with a standard wrench and inserting the new one. The used cartridge can then be cleaned by emerging it in a descaling solution, inspected, and reused.
This allows easy cleaning and service without removing the station from its installed location in food processing and other industrial facilities. The impact of production downtime can severely affect your bottom line. To maximize your uptime, be sure to have a spare STVM® cartridge assembly readily available to keep your operation running smoothly.
See the STVM® Washdown Station for information on our complete station.
Design Features
- Exclusive self-actuating Thermoloid® wax blend thermal actuator
- Easily interchangeable cartridge with a single moving element
- Corrosion-resistant – long service life
- Designed to minimize scaling
- Available in stainless steel or brass construction
Benefits
- Simplifies installation and maintenance procedures
- Minimizes downtime by allowing you to service the station in the field
- Reduced noise
- Can be cleaned and reused
Ordering
| |
| Valve cartridge assembly (150ºF (65.6°C)) Brass/Bronze |
| Valve cartridge assembly (185ºF (85°C)) Brass/Bronze |
| Valve cartridge assembly (150ºF (65.6°C)) Stainless Steel |
| Valve cartridge assembly (185ºF (85°C)) Stainless Steel |
Operation
Because of the unique mixing characteristics inside the STVM® steam mixing valve, it is capable of mixing steam and water without the usual noise and vibration associated with other types of mixers, eliminating operator stress, and making it ideal for workplace environments.
The unique flow characteristics of the vortices inside the valve create a scouring action that minimizes the effects of mineral deposits on valve operation, assuring increased service life even under adverse conditions. As a safety feature, the thermal actuator in the valve outlet is designed to turn off the steam flow into the valve if the cold water flow into the valve is interrupted.
The entire internal operating mechanism (cartridge) of our STVM® industrial steam water mixing valves can be quickly and easily removed as a single assembly by simply unscrewing the valve cap. This allows easy cleaning and service without removing the valve from the line.
See the STVM® Washdown Station for information on our complete station.
Typical Applications
Our steam mixing valve delivers hot water for batch fill operations, spray cleaning systems for vessels, commercial laundry hot water, boiler water preheating, de-aerating, and other direct steam injection heating applications.
Steam Water Mixing Valve Design Features
- Exclusive self-actuating Thermoloid® wax blend thermal actuator
- Corrosion-resistant – long service life
- Stainless-steel or brass valve body
- Interchangeable cartridge
- Over-temperature safety shutoff to protect personnel/equipment
Benefits
- Self-operating – no external power source required
- Reduced noise
- Reduction of maintenance and labor time
- Easy installation
- Designed to minimize scaling
Ordering
| |
| 1” STVM®-150°F Valve Bronze |
| 1” STVM®-185°F Valve Bronze |
| |
| |
Operation
The EcoFlow® mechanical seal support system contains a highly reliable and repeatable thermal actuator that continuously senses the seal water temperature. If the seal water should exceed the specified factory set-point, the valve will modulate open discharging the hot water, displacing it with cool water. This cooler water will cause the EcoFlow® to modulate closed. This cycle will continue to occur as long as excessive heat is transferred to the seal water causing the water temperature to exceed the valve’s factory set-point.
Typical Applications
The EcoFlow® valve is installed on the seal water outlet of a mechanical seal to maintain a constant seal water outlet temperature. This increases seal life by ensuring an optimum seal environment while drastically reducing water consumption and significantly increasing cost savings.

Design Features
- Exclusive self-actuating Thermoloid® wax blend thermal actuator
- All Stainless-steel body, fittings, spring, and plug
- Corrosion-resistant – long service life
- Ram-type plug for tight, reliable shutoff
- Operates in a narrow temperature band
- Unaffected by pressure variations
- Fail-safe design – fails open
- Optional side port feature allows flushing debris from inside valve
Benefits
- Self-operating – no external power source required
- Drastically decreases seal water consumption
- Increases water treatment efficiency
- Eliminates dry runs due to operator error
- Increases seal life
- Expands mechanical seal use to more applications
- Decreases operating cost
- Quick and easy installation
Seal Water Savings Example
To illustrate the water savings from the case study below that can be realized with EcoFlow‘s mechanical seal support system, we’ve used a typical seal manufacturer’s recommendation of 2.6 GPM to be used to flush the seals versus EcoFlow’s 0.05 GPM, operating 8 hours a day, 5 days a week (2080 hours per year).
Recommended: 2080 hours x 2.6 gallons per minute x 60 minutes = 324,480 gallons of water per year.
W/ EcoFlow: 2080 hours x 0.05 gallons per minute x 60 minutes = 6,240 gallons of water per year.
In our calculation, EcoFlow® can save ~318,000 gallons of water per year.
Read the complete case study: EcoFlow Sugar Produce Case Study
Ordering
| |
| |
| 1/4” EcoFlow® SS w/ side port |
| |
| 3/8” EcoFlow® SS w/ side port |
Operation of Passenger Rail Car Freeze Protection Valves
The ¾” thermostatic GURU PC® valve is installed at the lowest point within the potable water-bearing system of a passenger rail car. Its primary function is to prevent water from freezing when the car’s heating system is turned off.
This self-operating freeze protection valve continuously monitors ambient temperatures. It will automatically drain the water tanks of the rail car if the external temperature drops to the valve’s set-point of 35°F (1.7°C). This preemptive action protects the system from freezing and prevents potentially costly damage.
When power and heat are restored to the rail car, the valve warms up and closes, enabling the water tanks to be refilled before the car returns to service. As the valve operates mechanically, it requires no electrical or air connections.
To expedite the refilling process after a valve activation, we recommend using our electric heater assembly. The heater attaches to the valve’s thermal actuator and quickly warms it once power is restored, allowing the valve to close promptly and the system to be refilled efficiently.
To avoid unnecessary activations and nuisance dumping, we suggest replacing the cartridge assembly every two years, particularly if tests reveal sluggish or marginal closing performance. We offer a replacement cartridge kit to facilitate easy replacement without removing the Tee Body.
The GURU PC® valve is NSF/ANSI/CAN 61 & 372 Certified for use in potable water systems and has been rigorously tested to withstand shock and vibration, ensuring durability in harsh conditions. Compact, reliable, and in-line serviceable for ease of maintenance, the GURU PC® valve is the ideal solution to protect the potable water systems in passenger rail cars, including toilet modules and galleys, from freeze damage.
Design Features
- Exclusive self-actuating Thermoloid® blend paraffin wax actuator
- Low lead brass/bronze
- Dual-port seals
- In-line serviceable
- Available with an electric heater assembly for quicker refills
Benefits
- Self-operating – no external power source required
- Eliminates costly freeze damage in a passenger rail car
- High flow design for rapid draining
- Easy installation
- Minimal maintenance required
- NSF/ANSI/CAN 61 & 372 Certified
- Shock & Vibration tested
Heater Assembly Features
- 2 LED lights for easy visual check of power and heater
- Fully encapsulated PC board
- Self-limiting heater
- No moving parts to wear
- Minimal electrical noise
- Easy installation/removal with one hand
- Heaters available: 120VAC/74VDC & 230 VAC
Operation
The 1″ thermostatic GURU PC® freeze protection valve is installed at the lowest point within the potable water-bearing systems on a passenger rail car to prevent the water from freezing when the car heat is turned off for switching locomotives or even brief layovers.
This self-contained freeze protection drain valve monitors ambient temperatures and will automatically drain the system if the air temperature falls to the valve’s set-point, 35°F (1.7°C), preventing burst piping and thousands of dollars in damage. Once the car heat is restored, the valve will modulate closed, allowing for the tank to be refilled before returning to service. Since the valve is completely mechanical, no electrical or air connections are required for the valve to operate.
To avoid a delay in refilling the water system and getting the passenger car back into service after a valve activation we recommend using our electric heater assembly. The heater attaches to the thermal actuator on the valve and will warm it up quickly once power is restored to the car. This allows the GURU PC® freeze protection valve to close and the potable water system to be refilled quicker after a drain occurrence.
NSF 61 Certified and shock and vibration tested, the GURU PC® is compact, reliable, and in-line serviceable for ease of maintenance.

Design Features
- Exclusive self-actuating Thermoloid® blend paraffin wax actuator
- Low lead brass/bronze
- Dual port seals
- In-line serviceable
Benefits
- Self-operating – no external power source required
- Eliminates costly freeze damage in a passenger car
- High flow design for rapid draining
- Easy installation
- Minimal maintenance required
- NSF 61/372 certified
- Shock & Vibration tested
Heater Assembly Features
- 2 LED lights for easy visual check of power and heater
- Fully encapsulated PC board
- Self-limiting heater
- No moving parts to wear
- Minimal electrical noise
- Easy installation/removal with one hand
- Heaters available: 120 VAC/74 VDC & 230 VAC